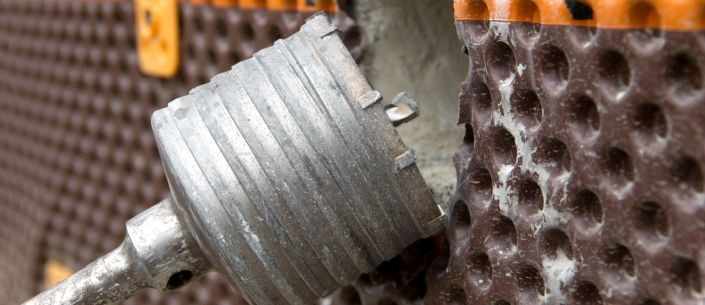
Core drilling is a critical process in construction, geology, and other industries, enabling precise cylindrical cuts in materials like concrete, asphalt, and rock. Whether installing utilities, creating structural openings, or extracting samples for testing, core drilling demands specialized techniques, tools, and adherence to best practices to ensure safety, quality, and efficiency. This guide explores the essentials of core drilling, drawing from industry insights to help professionals achieve optimal results.
Core Drilling Techniques
Core drilling techniques are designed to deliver precision and durability, particularly when working with challenging materials. Key methods include:
Machine Driven (MD) Drilling: Utilizes powerful machines to drive drill bits through tough surfaces, ensuring consistent and accurate cuts. This technique is ideal for large-scale construction projects requiring deep or wide holes.
Diamond Core (DC) Drilling: Employs diamond-tipped bits for superior cutting through hard materials like concrete and rock. DC drilling is highly accurate and minimizes material damage, making it a preferred choice for structural applications.
Inverted Drilling: Used when access from above is limited, this technique involves drilling upside down, often with hydraulic core drills that can operate underwater or in confined spaces.
These techniques are tailored to specific project needs, with MD and DC drilling being the most common in construction due to their reliability and precision.
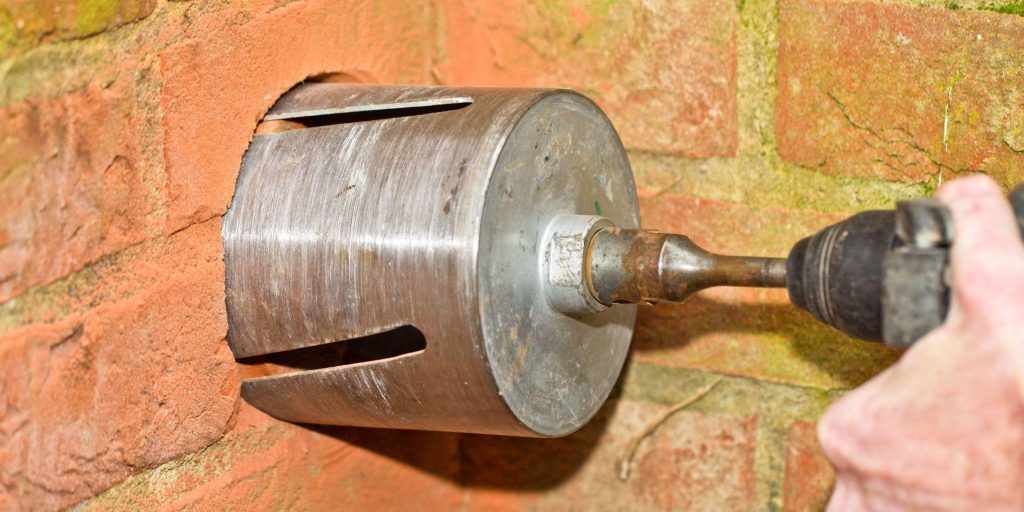
Essential Tools for Core Drilling
The right tools are crucial for effective core drilling. Modern equipment is designed to handle diverse materials while prioritizing safety and efficiency. Key tools include:
Diamond-Tipped Core Drills: These are the go-to choice for cutting through hard materials like concrete, granite, and limestone. Their durability and precision make them indispensable for high-quality results.
Specialized Drill Bits: For softer materials like wood or asphalt, specific bits are used to optimize cutting speed and prevent damage to the material or equipment.
Advanced Drilling Machines: Modern core drills feature variable speed controls, integrated depth sensors, deadman controls (which stop the drill if the operator loses control), and dust collection systems. Hydraulic core drills are particularly effective for inverted or underwater drilling, offering flexibility in challenging environments.
Retrieval Tools: Specialized tongs and extractors ensure intact core samples are retrieved without damage, critical for testing purposes in construction and geology.
Masonry Saws with Diamond Blades: Used for preparing core samples by trimming rough edges, ensuring they meet testing standards.
The choice of tools depends on the material, project scale, and environmental conditions, such as wet or dry drilling.
Best Practices for Core Drilling
To maximize safety, quality, and efficiency, core drilling requires adherence to best practices across three key areas:
Safety
Core drilling involves risks like flying debris, dust exposure, and equipment malfunctions. To mitigate these:
Training and Certification: All workers should undergo comprehensive training on equipment operation, safety protocols, and emergency procedures. Proper training reduces accidents and ensures compliance with industry standards.
Personal Protective Equipment (PPE): Always wear appropriate PPE, including hard hats, safety goggles, dust masks, hearing protection, and steel-toe boots. These protect against common hazards like debris and noise.
Dust Control Measures: Use water-fed drills or dust extraction systems to minimize airborne dust, which can pose health risks and reduce visibility. This is especially critical during dry drilling, where dust buildup can cause equipment to jam.
Equipment Inspection and Maintenance: Inspect tools for damage or defects before use. Ensure a tight fit between the driller and shaft, and keep a fire extinguisher nearby for emergencies.
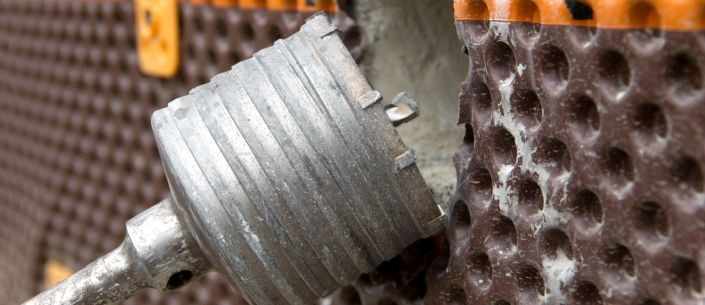
Quality
Achieving high-quality results in core drilling requires precision and attention to detail:
Bit Selection: Choose the appropriate drill bit based on the material. For example, diamond-tipped bits are ideal for concrete, while softer materials require specialized bits to avoid excessive wear.
Speed Adjustment: Drill at optimal speeds—slower for hard materials like concrete to prevent overheating, and faster for softer materials like asphalt to improve efficiency.
Monitoring and Adjustment: Continuously monitor bit condition, alignment, and hole quality during drilling. Adjust as needed to maintain precision and avoid issues like core jamming or uneven cuts.
Efficiency
Efficient core drilling saves time and resources while maintaining high standards:
Planning and Organization: Ensure all materials, equipment, and personnel are ready before starting. Clear the work area to avoid obstructions and streamline operations.
Leveraging Technology: Use advanced machines with features like depth sensors and dust collection to reduce manual labor and improve accuracy.
Maintenance and Calibration: Regularly service and calibrate drilling equipment to prevent breakdowns. Replace worn drill bits promptly to maintain cutting efficiency and avoid delays.
Additional Tips and Troubleshooting
Beyond the core practices, consider these tips to enhance core drilling performance:
Preventing Core Jamming: In wet conditions or during winter months, moisture in materials like bricks can increase the risk of core jamming. Use a safety clutch and side handle to prevent machine kickback, and clear dust regularly to avoid buildup.
Monitoring Slurry: When drilling through asphalt or concrete, watch for changes in the slurry (the mixture of water and cuttings). A change in slurry appearance indicates the drill has passed through the material into the base layer, signaling completion.
Barrel Longevity: Core bits typically last 10-15 meters, depending on material hardness, drill power部分
Waterproof Grease: Apply waterproof grease to the drill spindle thread to make bit changes easier and prevent corrosion, especially in wet drilling conditions.
Industry Applications
Core drilling is versatile and widely used across industries:
Construction: For installing HVAC ducts, sprinkler systems, plumbing, or electrical conduits. It’s also used to create openings for structural modifications or to extract samples for testing compressive strength.
Geological Exploration: To obtain core samples for analyzing rock formations or mineral deposits, providing critical data for mining and research.
Oil and Gas Exploration: While less relevant to construction, techniques like percussion drilling share similarities with core drilling and are used to extract samples from unconsolidated formations.
Learn More with Concrete Insight
Core drilling is a powerful technique when executed with the right tools and practices. For a comprehensive guide on mastering core drilling, including in-depth insights on safety, quality, and efficiency, visit Concrete Insight. Their expert resources can help you elevate your core drilling projects to the next level.
Write a comment ...